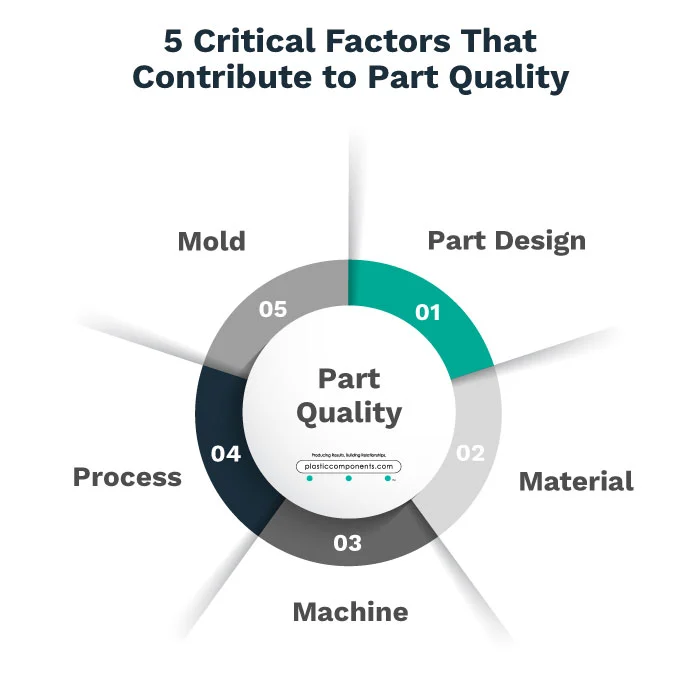
Home – Integrated Solutions Ensuring Precision and Efficiency
In the world of manufacturing, moulds and tools play a critical role in shaping and defining the final product. Quality control (QC) in mould and tool making is paramount, ensuring these tools meet precise specifications and deliver consistent, high-quality results throughout their lifespan. Here’s a deep dive into the importance and different aspects of QC in this vital industry:
Why is Quality Control Important in Mould and Tool Making?
- Dimensional Accuracy: Moulds and tools must be machined to exact specifications to ensure the produced parts match the design perfectly. Deviations in size or shape can lead to defective products, requiring rework or scrap.
- Surface Finish: Moulds and tool surfaces directly impact the aesthetics and functionality of the final product. QC ensures a smooth, blemish-free surface for optimal part quality.
- Functionality and Performance: Moulds and tools need to function flawlessly during the production process. QC verifies proper operation, including factors like material flow, cooling channels, and ejection mechanisms.
- Durability and Longevity: High-quality moulds and tools should last for thousands of production cycles. QC helps identify potential weaknesses and ensures the tools are built to withstand wear and tear.
Cost-Effectiveness: Preventing defects and rework through robust QC saves manufacturers time, money, and material waste in the long run.
Key Stages of Quality Control in Mould and Tool Making:
Design Review: The QC process begins with a thorough review of the mould or tool design. This involves checking for dimensional accuracy, manufacturability, material compatibility, and potential areas for improvement.
Material Inspection: QC ensures incoming materials used for mould and tool construction meet the specified standards. This includes checking for material properties, certifications, and potential defects.
Machining and Fabrication: Throughout the machining and fabrication process, QC procedures are implemented to verify dimensional accuracy, surface finish, and adherence to design specifications. Inspection tools like calipers, micrometers, and coordinate measuring machines (CMMs) are commonly used.
First Article Inspection (FAI): Once the mould or tool is complete, a first article inspection (FAI) is conducted. This involves creating a sample part using the new tool and comparing it meticulously to the original design specifications for any discrepancies.
Trial Run and Production Monitoring: During the initial production run, the mould or tool’s performance is closely monitored. This includes checking for proper part quality, cycle times, and any signs of wear or malfunction.
Ongoing Maintenance and Inspection: Regular maintenance and inspections are crucial to ensure the mould or tool continues to produce high-quality parts throughout its lifespan. QC procedures monitor for wear and tear, potential damage, and the need for preventative maintenance.
Advanced Quality Control Techniques:
3D Scanning: 3D scanning technology can be used to compare the final mould or tool with the original CAD model, identifying any dimensional deviations.
Computer-Aided Inspection (CAI): CAI software analyzes data from CMMs and other inspection equipment, providing detailed reports on dimensional accuracy and potential issues.
Non-Destructive Testing (NDT): NDT techniques like X-ray or ultrasound can be used to inspect internal features of moulds and tools for hidden defects or potential weaknesses.
Benefits of a Robust Quality Control System:
Reduced Production Costs: By preventing defects and rework, robust QC minimizes material waste and production delays, leading to overall cost savings.
Improved Customer Satisfaction: Consistent production of high-quality parts ensures customer satisfaction and reduces the risk of product recalls.
Enhanced Brand Reputation: A commitment to quality control builds trust and strengthens a company’s reputation within the industry.
Increased Efficiency: Streamlined QC processes identify issues early on, preventing production bottlenecks and downtime.