What is Plastic Mould Flow Simulation ?
Plastic Mold Flow Simulation is a computer-aided engineering (CAE) technique used in the plastic injection molding process. It involves the use of specialized software to simulate and analyze how molten plastic material flows within a mold cavity during the injection molding process. This simulation provides insights into various aspects of the molding process, helping designers, engineers, and manufacturers optimize their designs, avoid defects, and improve overall product quality.
The process in which we can see the actual behavior of molten plastic in actual working condition of mould with the help of various simulation CAD software ( Mold Flow).
The software digitally simulates every aspect of the manufacturing process from material flow, cooling, shrinkage, and warpage of the plastic part.
With the help of the simulation software, we save time and cost of during manufacturing.
This software gives us a complete detailed report of the product with the exact defect and the actual parameters to be considered during the process.
Plastic mould flow simulation is a powerful tool used in the plastic injection molding industry to optimize designs, minimize defects, reduce manufacturing costs, and improve the overall quality of plastic products.
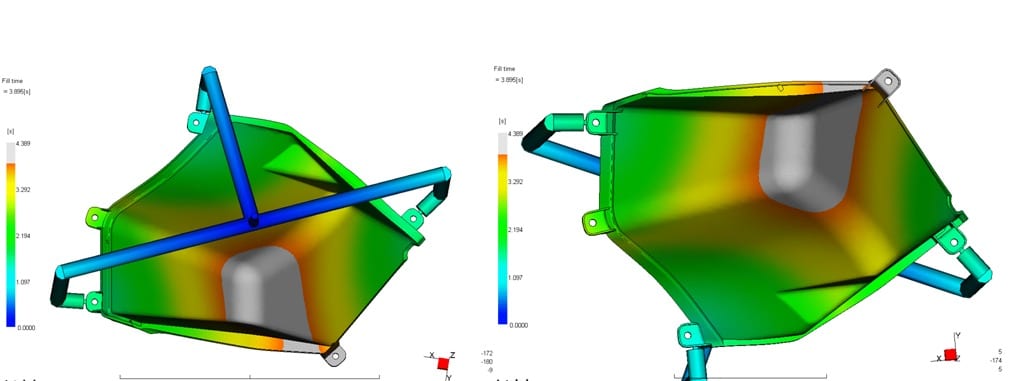
Area where we use flow simulation:
Design Optimization: Our Design team uses this process to optimize the flow before performing a quality check. Plastic mold flow simulation allows designers to test and optimize various design aspects, such as gate placement, runner design, and part geometry. By simulating how plastic material flows and fills the mold, designers can identify potential issues like air traps, weld lines, and uneven filling. This information helps them make informed design decisions to minimize defects and ensure uniform filling.
Predicting Defects: The simulation can predict potential defects that might occur during the molding process, such as warpage, sink marks, voids, and excessive shrinkage. This information enables engineers to make adjustments to the mold design, material selection, or process parameters to mitigate or eliminate these defects before manufacturing.
Cycle Time Optimization: Mold flow analysis can assist in optimizing cycle times by identifying areas where cooling might be inefficient or where the plastic takes longer to solidify. Reducing cycle times can lead to increased production efficiency.
Gate and Runner Design: The positioning and design of gates (the entry points for molten plastic) and runners (channels that distribute plastic to the mold cavities) significantly influence the molding process. Simulation helps determine the optimal gate size and location for balanced filling, reduced pressure drop and minimized part defects.
Mouldability Analysis: Before committing to expensive mold production, mold flow simulations can assess whether a design is moldable and can be manufactured with the desired quality. This prevents potential manufacturing issues and costly modifications after the mold is built.
Integrated Solutions offers all types of flow simulation analysis by our expert professional team to ensure your mould works perfectly.