
Rubber Mould | Manufacture & Design
Rubber tools Or Rubber Made Products manufacturing involves the production of various tools and equipment made from rubber materials.
Rubber is a versatile material that offers unique properties such as flexibility, durability, and resistance to corrosion, making it ideal for a wide range of tools and equipment. Here are some examples of rubber tools and their uses:
- Rubber mallets: Rubber mallets are commonly used in construction and woodworking to strike materials without causing damage or leaving marks.
- Rubber gaskets: Rubber gaskets are used in various industries such as automotive, aerospace, and plumbing to create a seal between two surfaces and prevent leaks.
- Rubber hoses: Rubber hoses are used in various industries such as agriculture, construction, and automotive to transport fluids and gases.
- Rubber pads: Rubber pads are commonly used in machinery and equipment to provide cushioning and vibration damping.
- Rubber rollers: Rubber rollers are used in various industries such as printing, packaging, and textiles to facilitate the movement of materials.
Rubber tools manufacturing involves a range of processes, including mixing, molding, extrusion, and curing. The manufacturing process may vary depending on the type of tool being produced and the specific requirements of the customer. Overall, rubber tools offer unique benefits and are widely used in many industries due to their versatility and durability.
Rubber molding is a process to convert unprotected rubber or elastomer into a useful product by transferring, compressing or injecting raw rubber material into a metal mold cavity. The applied pressure creates a chemical reaction, such as curing or vulcanization, that causes the polymer chains in the material to crosslink.
All rubber manufacturers use heat and pressure to produce their products. The most common methods for rubber molding are injection, compression, and transfer. With the continuous development of products, rubber mold manufacturers are constantly adjusting to meet the growing demand for grommets, gaskets, tubing, O-rings and hoses.
Rubber products and components are produced, shaped and formed using the molding process. Molding is used, in addition to shaping parts, to subject rubber materials to chemical processes that harden or harden the polymer chains of raw rubber. The chemical reaction forces the long polymer chains to crosslink, which prevents them from moving freely. Rubber material expands and contracts as stress is applied or eliminated.
There are several steps that need to be taken prior to initiating the molding process.
Rubber can be molded into complex shapes, geometries and designs. During the design process, the configuration is incorporated into the rubber geometry that is used to make the production of the final product more economical. In molding part design, engineers have to calculate the part line and its location, which should have a minimum draft angle. Mold design is the foundation of part development and can determine the success or failure of parts production.
Compression molding is the simplest type of rubber molding process. A two part clamshell style mold is used to shape the final piece. Once the un-vulcanized rubber is placed in the mold cavity, the mold is closed and heated. The pressure is created using a hydraulic press. As the rubber in the mold heats up, it fills the mold cavity. When the proper temperature is reached, the rubber vulcanizes, or hardens, which ensures that the rubber will keep its shape as it cools in the mold.
The transfer molding process is similar to the compression molding process, but uses a transfer system that takes place at the top of the mold that feeds the raw rubber into several mold cavities after the press is closed. Before being forced into the mold cavity, rubber compound is placed in the part of the mold called the pot. From the pot, the compound is forced into the mold cavity by a hot plunger or piston through a small part of the mold called a sprue. Transfer molding is a highly efficient process with short tool loading times. The process allows for a high production run, although the parts do not have tight tolerances. When curing is complete, the mold is split, and the parts are discarded.
The injection molding process is used to produce products that require tight tolerances with high precision and accuracy. The injection process begins by heating the raw rubber to make the liquid such that it flows more freely and smoothly into the mold cavity. The preheating process shortens the curing time and allows for higher curing temperatures. The nature of injection molding requires that the mold be clamped tightly, which helps to avoid or limit flashing. Rubber for injection molding is supplied into the mold through a nozzle and barrel assembly that provides a continuous flow. The rubber fixture, referred to as the glue stock, enters the mold cavity through a gate after traveling through a system of sprays and runners. The liquefied rubber fills the cavity of the mold and packs tightly onto the walls of the mold to form the desired shape.
Our Manufactured Mold Gallery


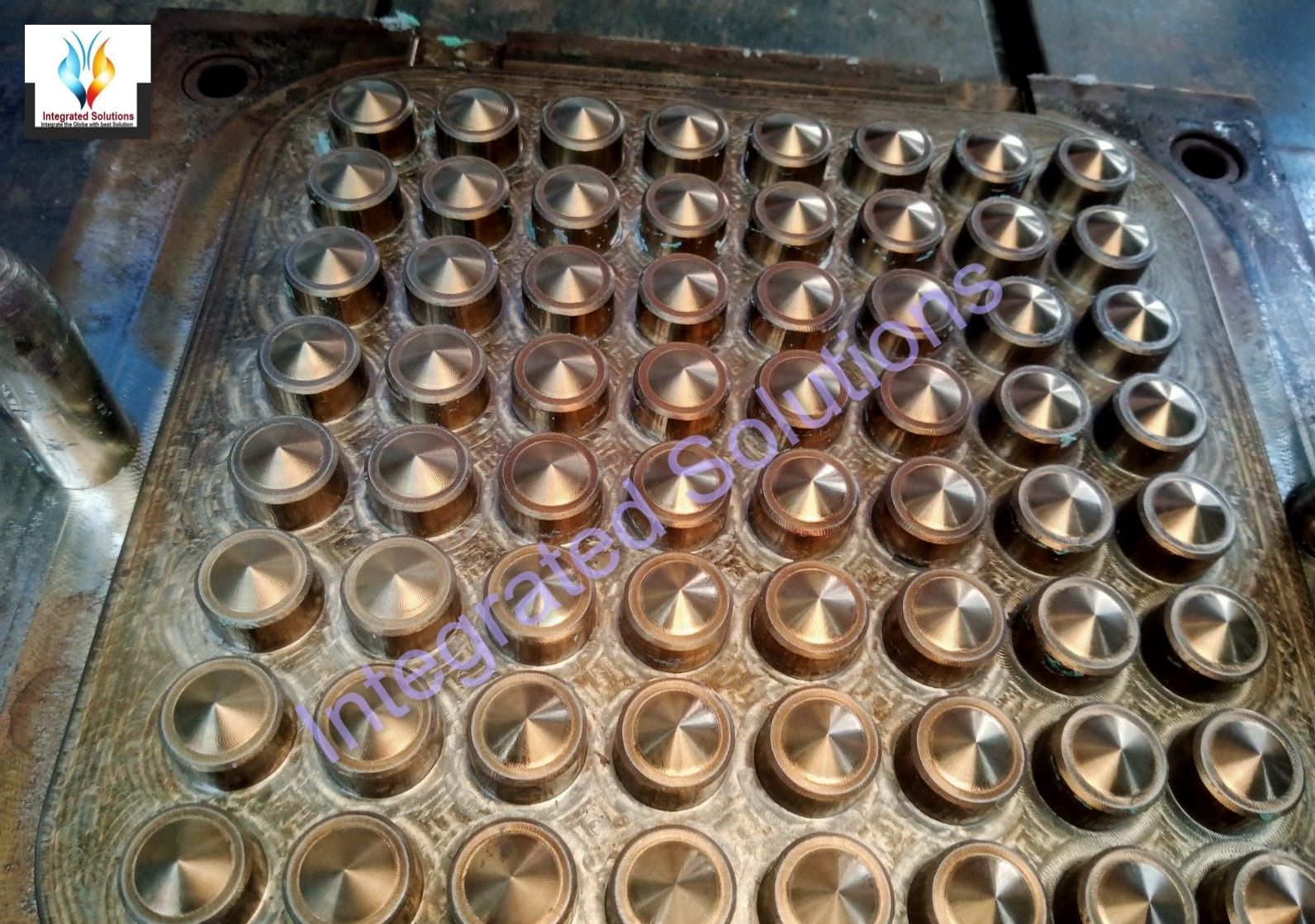
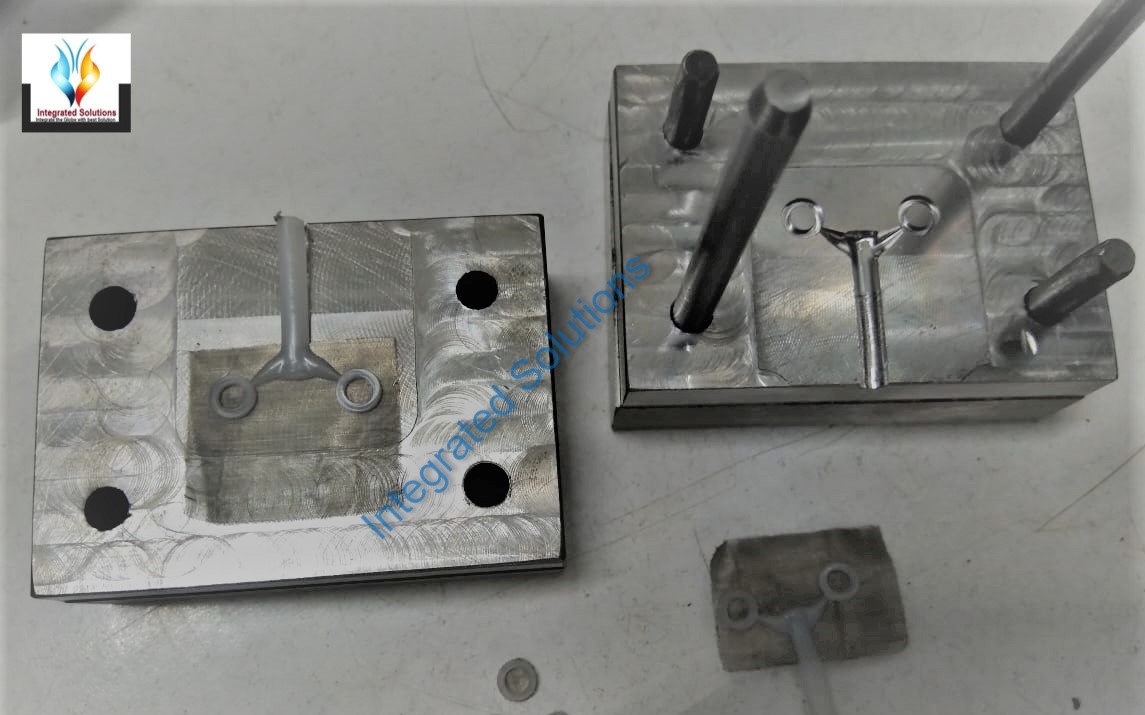



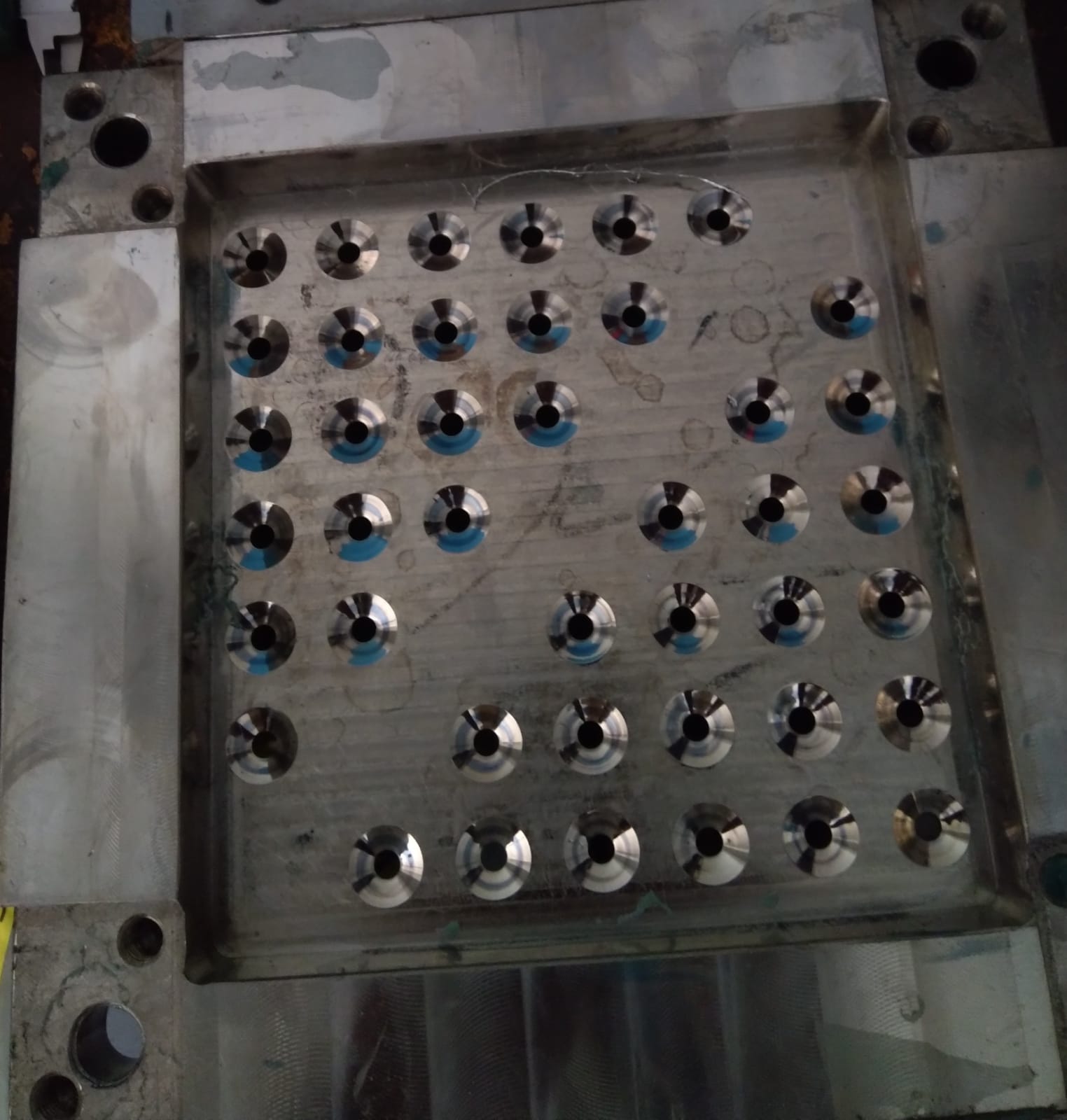
O-ring Rubber Mould
Integrated Solutions manufactures O-ring Mould that is used in a wide variety of applications, including hydraulics, pneumatics, and automotive. We cater to almost all automotive companies in Gurgaon and Delhi -NCR. Our Products are third-party quality-verified and tested on every parameter to fulfill the exact need.
An O-ring in a rubber mold is a circular gasket that is used to create a seal between two or more parts. It is made of a soft, elastic material, such as rubber, and is designed to conform to the shape of the parts it is sealing.
To make an O-ring in a rubber mold, the first step is to create a mold cavity that is the exact shape of the desired O-ring. This can be done by machining a metal mold or by using a 3D printing process. Once the mold cavity is created, the next step is to inject a liquid rubber compound into the mold. The rubber compound is then cured, or vulcanized, to harden it. Once the rubber is cured, the O-ring can be removed from the mold.
So we manufacture such O-ring Mould that produces the same required products. We maintain consistency and accuracy at the same time.
We manufacture many different types of O-ring Mould to cater to all sector’s requirements such as:
- EPDM: EPDM is a synthetic rubber that is resistant to water, chemicals, and ozone. It is a good choice for applications where the O-ring will be exposed to these elements.
- Nitrile: Nitrile is a synthetic rubber that is resistant to oil and fuels. It is a good choice for applications where the O-ring will be exposed to these fluids.
- Viton: Viton is a synthetic rubber that is resistant to a wide variety of chemicals, including acids and bases. It is a good choice for applications where the O-ring will be exposed to these chemicals.

U-Seal Rubber Mould

U-Seal Rubber Mold
Material : Steel
Application : Rubber U-Seal
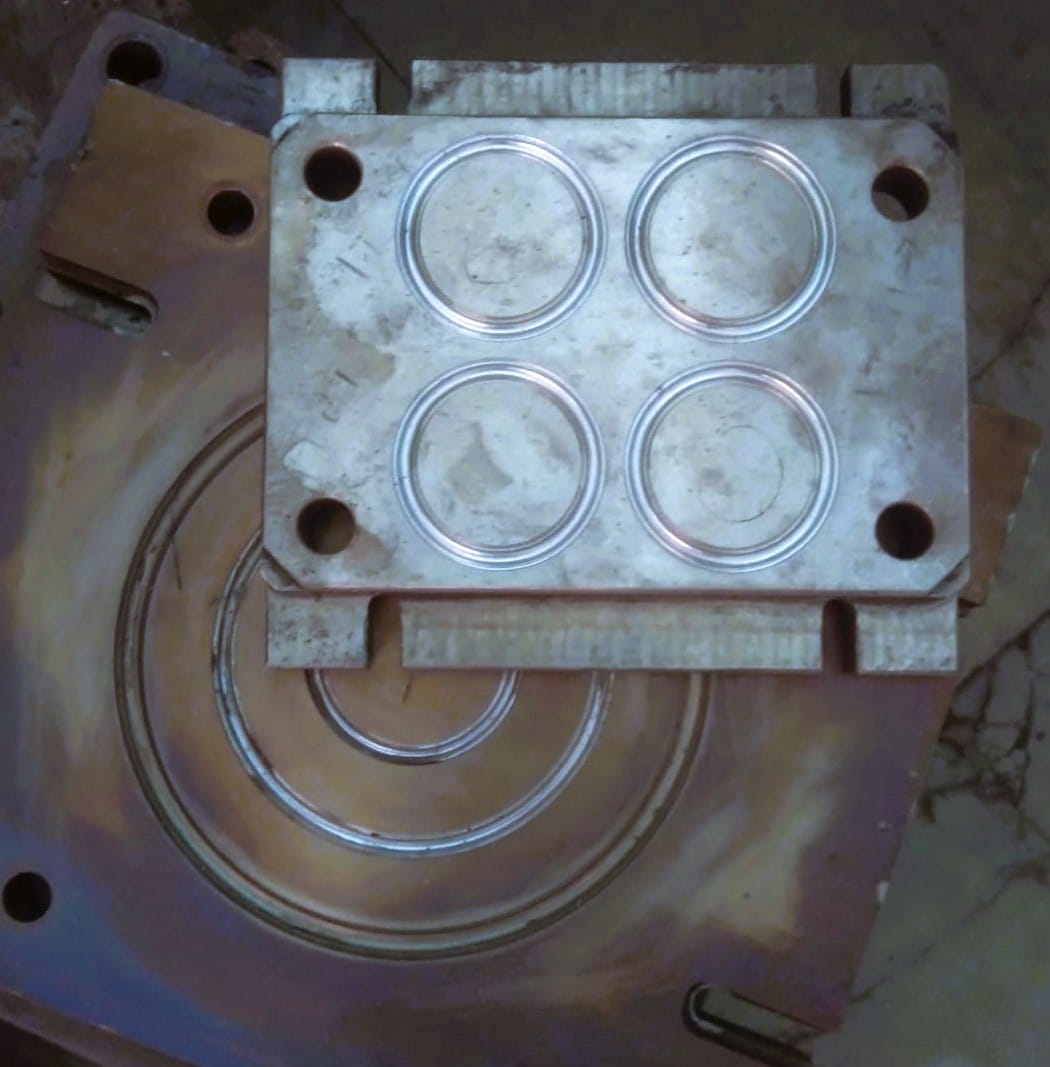
U-Seal Rubber Mold
Material : Steel
Application : Rubber U-Seal

U-Seal Rubber Mold
Material : Steel
Application : Rubber U-Seal